Pharmacy compounders have a lot of factors to consider when making the decision to go into the business of mixing individual prescriptions, particularly those considered “hazardous.” It can be a lucrative operation, but one which is closely overseen. For good reason, though: mistakes in the recent past have taught us that sloppy procedures, partly resulting from a lack of regulations, can have deadly consequences.
Once you’ve make the commitment to move forward with your compounding pharmacy business model, you have to understand your responsibilities (and the associated costs) regarding equipment and furnishings. What used to be true for minimum “engineering controls” is no longer good enough, and regulators will make sure that pharmacies comply.
Click here for more USP resources. Find out what is required, based on the types and quantities of drugs you plan to formulate. It’s also interesting to note the areas where final decisions have yet to be made or enforced.
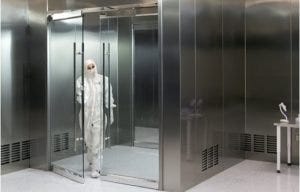
Terra’s BioSafe® steel cleanroom with non-contaminating glass doors.
Let’s assume that you need a cleanroom, also known as a “secondary engineering control” (SEC) to house your compounding aseptic isolator (CAI) or laminar air flow workstation (LAFW), also called “primary engineering controls” (PEC). For 503B outsourcing pharmacies performing sterile compounding, the minimum requirement is an ISO 5 buffer room with an ISO 7 antechamber (gowning area). If you are performing sterile compounding in a traditional 503A pharmacy, an ISO 7 buffer room with ISO 8 antechamber is needed. Click here for a quick ISO refresher.
Terra Universal makes USP 797 and USP 800 cleanrooms that meet these cleanliness requirements. They are turnkey solutions; present your own required specifications along with the type of compounding you will perform, and a Product Specialist will help you design and build your room. While the rooms comply with the minimum regulation requirements, you can always increase the ISO rating simply by adding additional HEPA or ULPA fan/filter units. It’s a relatively small price to pay for some insurance and peace-of-mind.
USP 797 Compounding Cleanroom
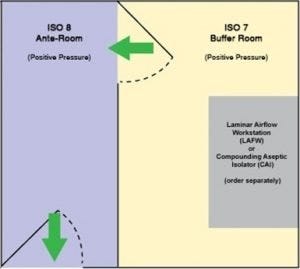
USP 797 floor-plan option. Both chambers hold positive pressure.
The modular, all-stainless steel construction of this positive-pressure room is a fast and convenient way to get your compounding business up-and-running. The ante-chamber meets ISO 8 requirements, while the buffer chamber complies with ISO 7. The snap-in-place steel wall panels form a double-wall construction that is both sturdy and insulating. As with any business, change is the norm. Don’t worry; modular components may be disassembled and reassembled to relocate or augment the room.
The turnkey solution includes fan/filters units (FFU) and fluorescent lighting, supported in a steel ceiling grid, plus an internal partition with bi-swing door that separates the buffer and ante chambers. Radius corners are specially designed for frequent, and efficient, wipe-downs. Magnehelic pressure gauges help monitor room conditions and differentials; exhaust ducts or FFU speed may be adjusted to bring the room to the required pressure.
Steel wall panels stand up to the abuses of frequent sterilization. They don’t outgas or shed particles, and retain no moisture. Windows are made of tempered glass, another cleanroom-friendly material that is not easily damaged. Laminar air flow fan modules can be upgraded from HEPA to ULPA filters. Add or replace other modules as needed: UV sterilizing lamps, ionizing bars, and LED lighting strips, to name some.
USP 800 Compounding Cleanroom
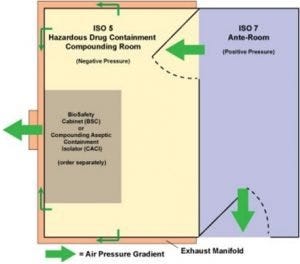
USP 800 floor-plan option: buffer room is negative pressure while ante chamber is positive pressure.
Like the USP 797 room, insulated stainless steel panels of the USP 800 room require no external bracing. The free-standing, turnkey room is the negative-pressure controlled space your lab needs to compound prescriptions using pharmaceuticals appearing on the NIOSH hazardous-drug list.
Negative pressure is created when the exhaust system pulls air from the room for safe dispersal. Terra’s exhaust manifold connects to your in-house duct system to direct contaminated air to the outside. Depending on the type of compounded drugs, you may have concurrent positive- and negative-pressure rooms, each with a different ISO rating. The rooms come with differential-pressure gauges to make conditions visible, allowing faster reaction time when adjustments are warranted.
The Food and Drug Administration (FDA) uses current Good Manufacturing Practices (cGMP) as the basis for enforcement of pharmacy compounding facilities. This quality assurance system is the standard and must be followed (see 21 CFR, parts 210 and 211). Terra’s USP 800 room meets these criteria; it is made of materials that do not promote the growth of microorganisms, and are designed for frequent decontamination.
Cleanroom Controls
USP 800 cleanrooms from Terra come standard with an Environmental Control System to help with both daily operations as well as routine inspections. A centralized touch-screen panel lets personnel monitor conditions and make adjustments. Sensors provide feedback to the
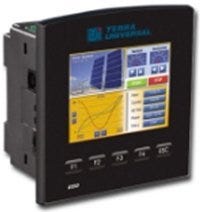
Cleanroom controls for system for automatic monitoring and adjustment.
system regarding pressure, temperature, humidity and air speed. Adjustments can be made directly to the touch-screen control panel, or remotely. Via an Ethernet connection, all data is logged for the traceability that all auditors demand, freeing personnel from time-consuming documentation.
Energy-saving night-mode can also be initiated during off-shift hours when fan/filter units don’t have to work at maximum capacity. Do this manually or automatically using the programmable clock-calendar.
Final Thoughts
Recent pharmacy compounding regulations have made compliance more challenging and expensive. Modular rooms, unlike bricks-and-mortar, don’t usually require building permits. They can also be constructed in a fraction of the time, and at a fraction of the expense. With modular alternatives that meet or beat the strict FDA requirements for drug compounding operations, maybe staying in the business is not such an impossible goal. After all, pharmacy compounding is a growing industry, with a projected 3% annualized increase (estimated to reach over $6B by 2020).
Click for more information about Terra’s USP 797 Compounding Cleanroom.