Considering the countless designs and operating regulations, specifying the right clean room for your application is not a simple 1-2-3 process. But as with other capital purchases, a checklist of critical questions can help guarantee a decision that meets your expectations. Here’s what our clean room specialists first evaluate when designing a controlled environment:
How will my clean room be used?
The processes taking place in a cleanroom determine functional characteristics. For instance, static sensitivity or chemical processing dictate specific types of construction materials. Perhaps your needs can be met with a softwall cleanroom that features full-view plastic panels, or maybe you need an all-steel modular cleanroom for ultimate cleanliness. The number of personnel, their frequency of access, approved garbing protocol and necessary application equipment have a significant influence on cleanroom design as well.
How much space is available?
Working space can be a significantly limiting factor when designing your clean room. Available ceiling height, for example, will influence ventilation, air conditioning costs, and the ease of replacing air filters. Additionally, some operations require gowning before workers enter the clean room; space constraints may dictate either an internal or external gowning room. An air shower may even be needed, depending on how clean the environment needs to be. For larger projects, engineering considerations become more apparent. Seismic analysis can assess which changes may need to be made in your design to ensure an overall stable operation.
Finally, very large modular rooms, with spans greater than 20 feet, will generally require internal support pillars or external bracing that entails a contractor and formal permitting process. Smaller rooms generally do not require these provisions and are therefore much faster and economical to bring online.
Which cleanliness rating does my application require?
Although each clean room operation typically involves its own unique protocol, the International Standards Organization (ISO) has set global classifications as a standard benchmark for cleanliness levels. ISO requirements specify the number of particles per cubic meter of air, which is maintained by a certain airflow velocity and air changes per hour. These standards let you calculate the quantity and location of FFUs within the clean room (Tables 1 and 2). The more stringent the cleanliness requirement, the greater the number of fan/filter units and the higher the initial and ongoing operational expense. After determining how many FFUs you’ll need, it’s important to space them evenly across the ceiling without clustering them together. Uneven air flow will disrupt laminar airflow uniformity, causing unwanted turbulence.
This commonly used equation helps decide the number of FFUs needed for your controlled environment:
No. of FFUs = (Air Changes/Hour ÷60) x (Cubic ft. in room÷ 650)
*650 represents the average cubic feet per minute (CFM) output of a loaded FFU at medium speed. Round up fractions to avoid under-performance
*Tables 1 and 2 based on IEST recommendations
What type of air pressure is needed?
The main variable that determines the type of cleanroom air pressure is whether the sample is to be protected from the surrounding environment, requiring positive pressure isolation, or whether personnel and the surrounding environment are to be protected from a harmful sample, requiring negative pressure containment. A positive pressure cleanroom maintains a uniform laminar flow (Figure 1), in which air is forced through filters located in the ceiling, and exits vents at the base of cleanroom walls. A negative pressure cleanroom removes hazardous chemicals or powders either by exhausting room air through the ceiling (Figure 2) or along the base of the wall (Figure 3).
Air flow and pressure are important to consider because they influence the physical space and energy consumption of your cleanroom. You may be subject to building permits or regulations, especially if the cleanroom design alters the structure of your facility or risks releasing harmful fumes into the environment.
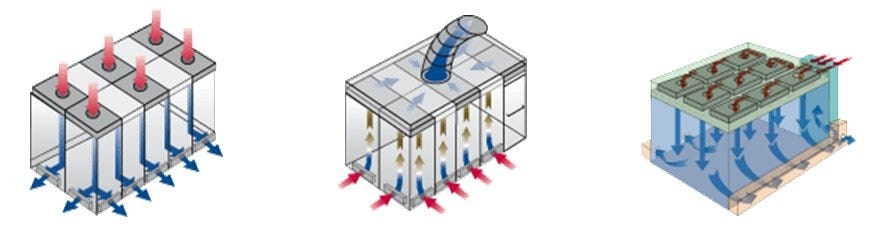
Figures 1-3, Left to Right: Positive pressure for isolation; Negative pressure venting for chemical vapors; Negative pressure with exhaust vents at the base of the wall for hazardous powders.
What other design considerations are integral to my specific application?
Just as assembly lines have a particular order for tasks, cleanroom protocol will influence positioning of doors, outlets, pass-throughs and other utilities. Swing doors or pass throughs, for instance, can be obstructed by equipment, so do you move the equipment, or relocate the door? If you anticipate moving large equipment in and out of the cleanroom, you may want to consider a removable wall. Some applications are best accommodated with roll-up or slide doors or oversized cart pass-throughs.
Likewise, some models of light fixtures can interrupt airflow uniformity. Consider installing tear-drop fluorescent fixtures or LED strip lights on the ceiling grid in-between FFUs to maintain laminar air flow. Your facility’s overall energy consumption and costs can benefit from these design options.
It may be necessary to assemble your modular room close to an existing lab, or designated manufacturing/testing areas. Since the cleanroom has its own power module, it only needs a ceiling-drop electrical connection; running wiring from a central power system is not difficult. However, if the cleanroom contains equipment requiring a source of water, such as hand-washing stations, plumbing is a consideration. PVC pipes can also be run overhead and dropped down to the room location, but drainage (perhaps to the existing plumbing system) should be planned prior to erecting the room.
Conclusion
After closely examining the major factors that influence how your cleanroom will be used, you may be faced with even more pressing questions. You can find helpful information from our Modular Cleanroom Design & Configurations. Terra has product specialists and engineers who can answer your application-specific questions. Give us a call or chat with us online today!